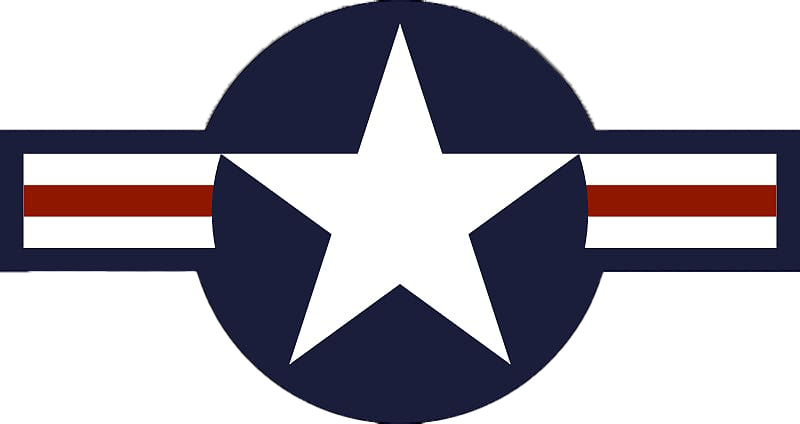
T-34 Mentor
Restoration
The decades of use, abuse, accidents, and neglect from the US military and civilian owners alike have left many T-34s in poor condition. Not only are many aesthetically unpleasant, the undetected problems lurking deep in the mechanical systems are much more dangerous. It is common to find chaffed wiring, loose hardware, broken pulleys, corroded fuel lines, failing bearings, frayed control cables, damaged structural components, even (this is true) a hammer and steel punch forgotten between the fuel bladder and wing skin (separate instances too). These are just some examples of dangerous items that cannot be discovered during a routine inspection. The best way to insure you will have a safe, reliable, long lasting aircraft is a full restoration. Blackwell Aviation cut its teeth on T-34 restorations, and have won over 30 national awards for our finished aircraft, including many in the warbird category at EAA’s Airventure. Our comprehensive process covers the entire aircraft, from spinner to tail cone.
We start by disassembling the entire aircraft. The engine is removed, interior stripped, wiring thrown out, wings taken off, until all that is left is the bare structure. Then the remaining airframe is painstakingly inspected for any corrosion or damage.
The interior is then stripped of all paint and coated with zinc chromate primer. The sheet metal work begins by replacing all of the cockpit side walls and floors, and new custom fit side consoles made from aluminum. Fuselage belly skins and side skins are replaced as necessary. All new metal and cockpit interior is then epoxy primed and painted. An entire new wiring harness is assembled from Mil-spec wire that is stamped with codes corresponding to wiring diagrams. The harness is installed and secured, and new connectors soldered in. Wires are terminated and connected to new switches and circuit breakers, and all new metal photo placards installed. New flight control cables and pulleys are routed, and new bearings installed in flight control actuator arms. New plumbing is meticulously bent and installed. Throttle quadrants are restored, trim actuators overhauled, flap and gear motors replaced, landing gear transmissions rebuilt, fuel valves resealed, and all new relays installed.
A complete avionics wiring harness is constructed, terminated, and bench tested before being installed. New RG400 antenna cables are routed through the fuselage. All new instruments and avionics are fit into custom laser cut instrument panels front and rear and plumbing connected. A full day of electrical testing and programming eliminates any major issues prior to the first flight.
The engine compartment (if not already done) is converted to accept the new Continental IO-550B or IO-550R. New engine mounts and forward structure are installed with precision jigs. The compartment is then stripped and painted to match the interior. New wiring, plumbing, ducts, and cables are installed..
The exterior of the aircraft is taken to bare metal and any sheet metal repairs made. Stabilizers and control surfaces are reskinned, primed, and painted. Wing spars are replaced with Beechcraft common spars. Wheel wells are stripped and painted white, and the wings and fuselage are painted to customer spec. Lettering and insignia is then carefully masked and topcoated. Canopies are re-glassed or replaced, and the frames are painted or polished.
After all paint work, the final assembly starts. Wings are bolted on, freshly rebuilt and painted landing gear installed and rigged, and wiring connected. Control cables routed, flight controls balanced and rigged, and autopilot servos connected. New fuel bags are installed and leak checked. A factory new engine is dressed out with new baffling, hoses, ignition harness, magnetos, starter, alternator, prop governor, and exhaust. The powerplant is lowered into place and secured with new mounts. All connections are made, and a new propeller is installed.
The end result is an aircraft that is better than it was new in performance, reliability, and appearance inside and out. All ADs and service bulletins are complied with, and logbooks and paperwork organized with the Adlog system. The aircraft can be flown with peace of mind, and your concerns will no longer be of dangerous conditions that may be hiding in an aging machine in disrepair. The only downfall will be your new obsession with keeping your fresh, show winning warbird spotless.
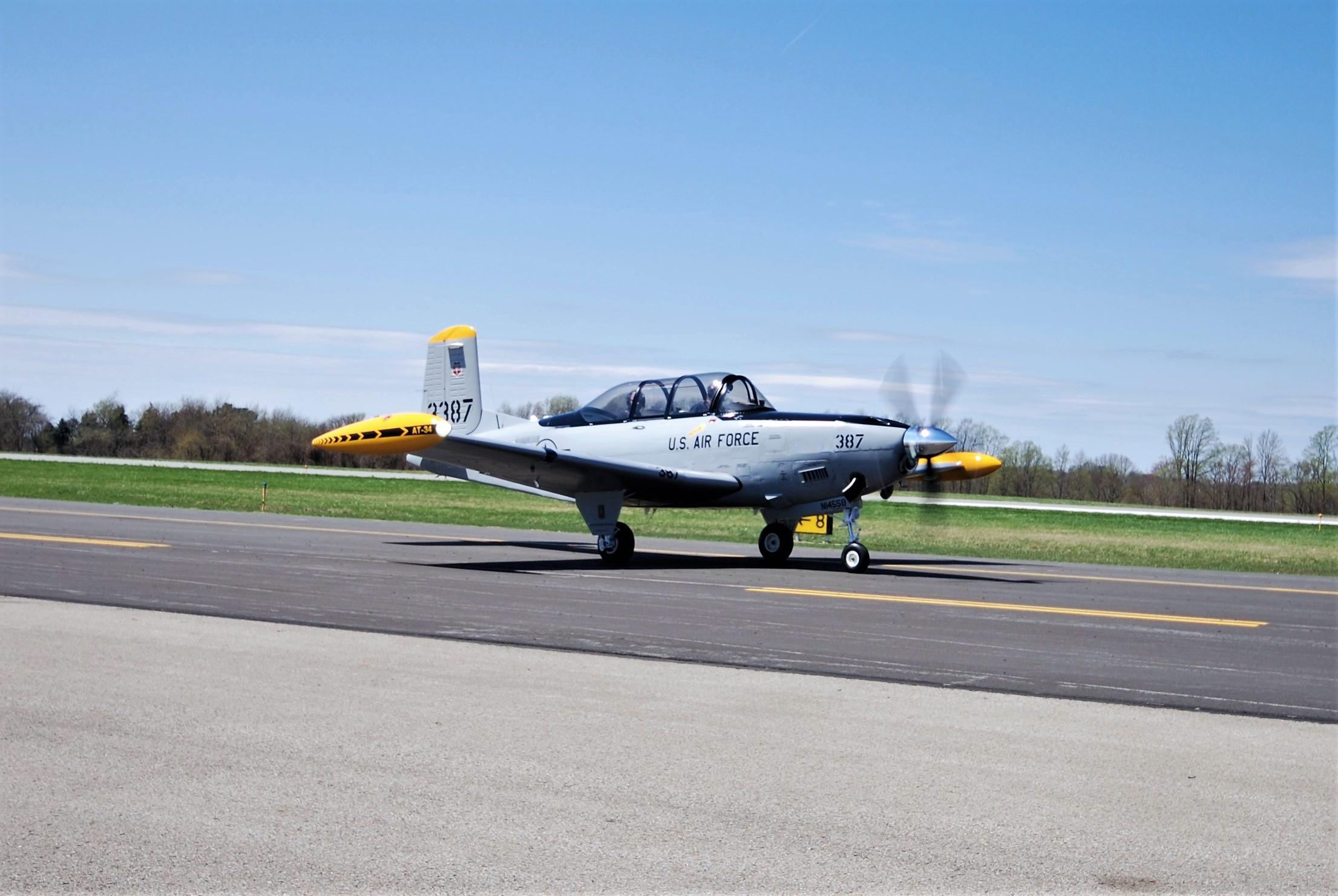
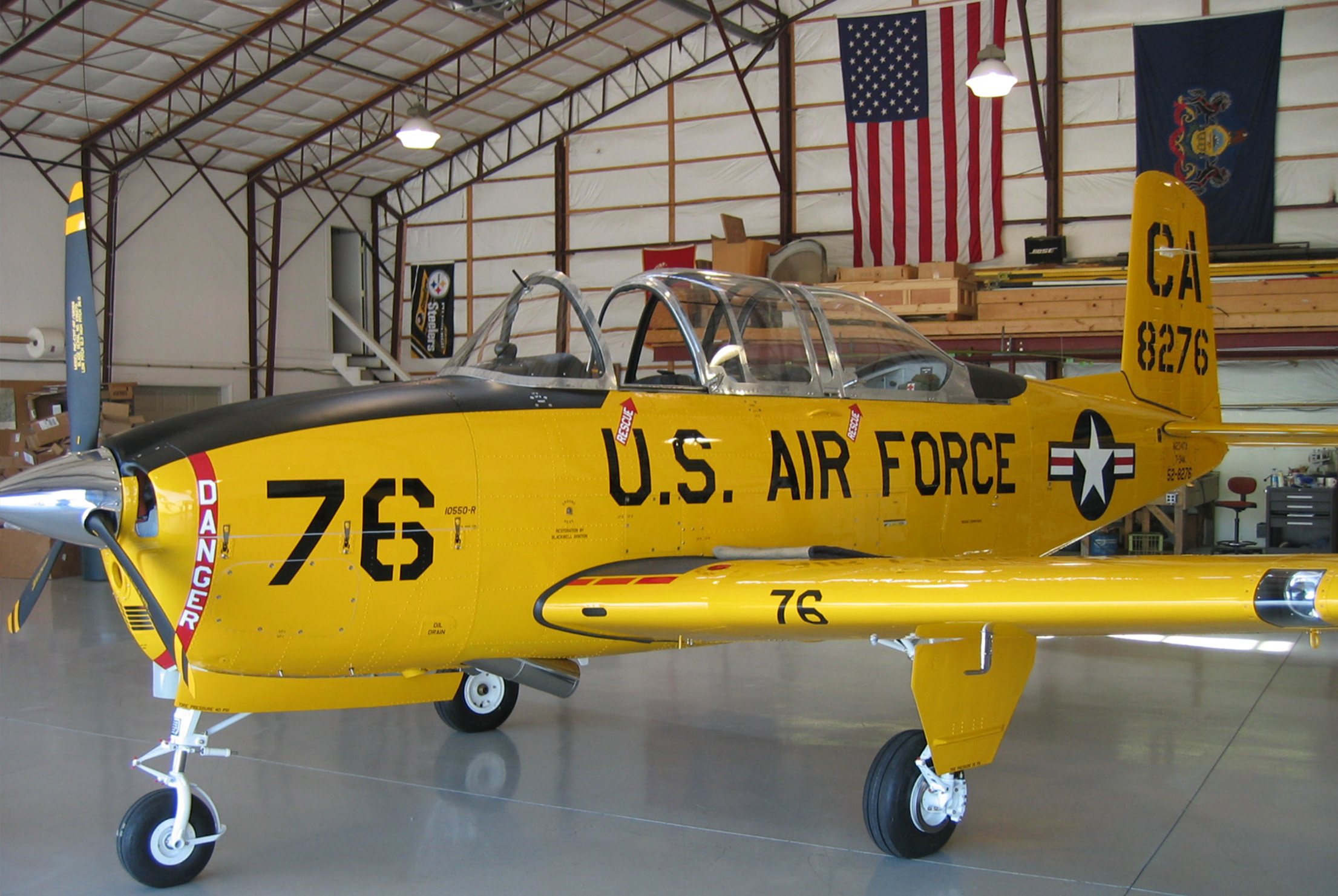
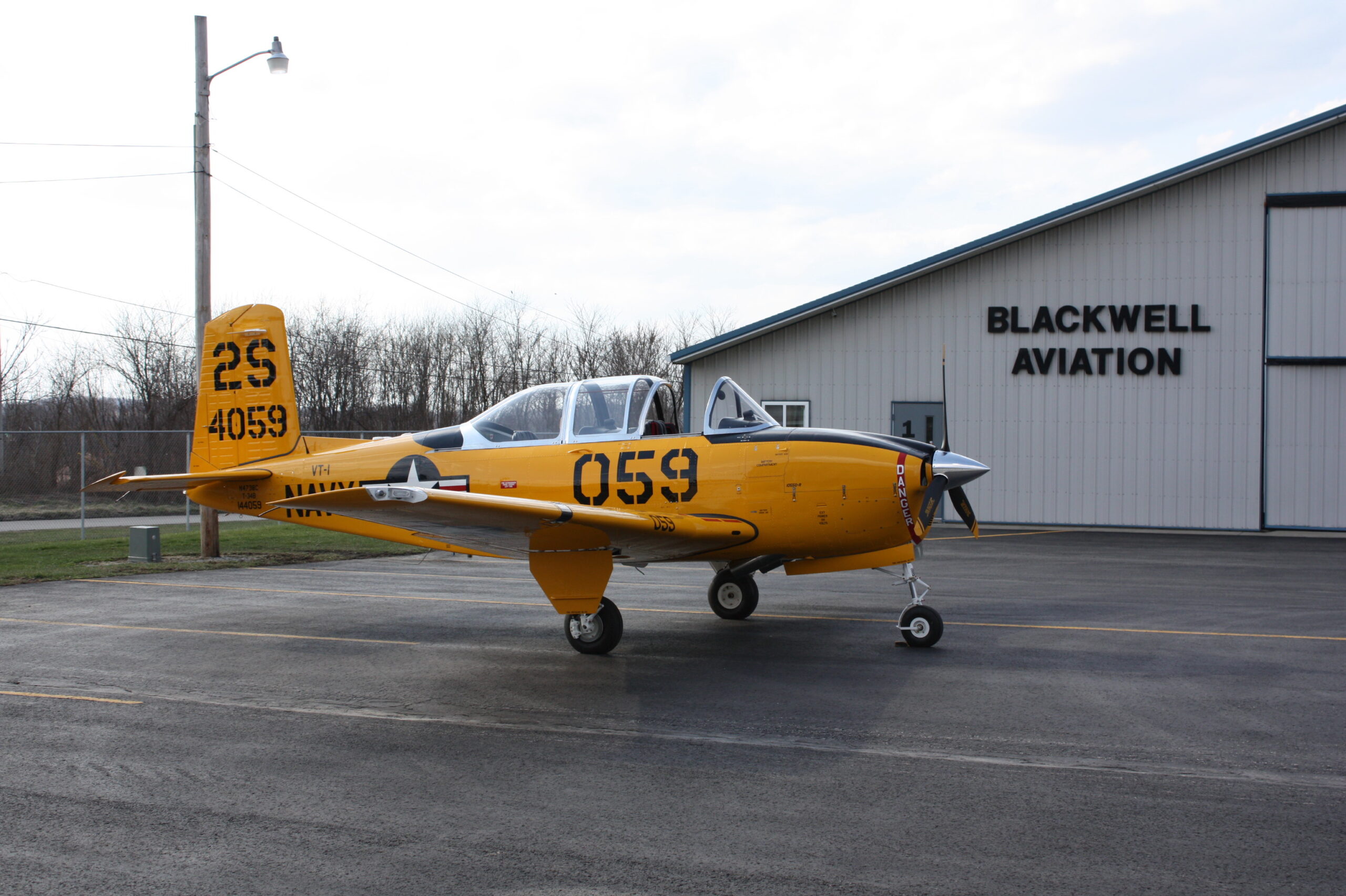
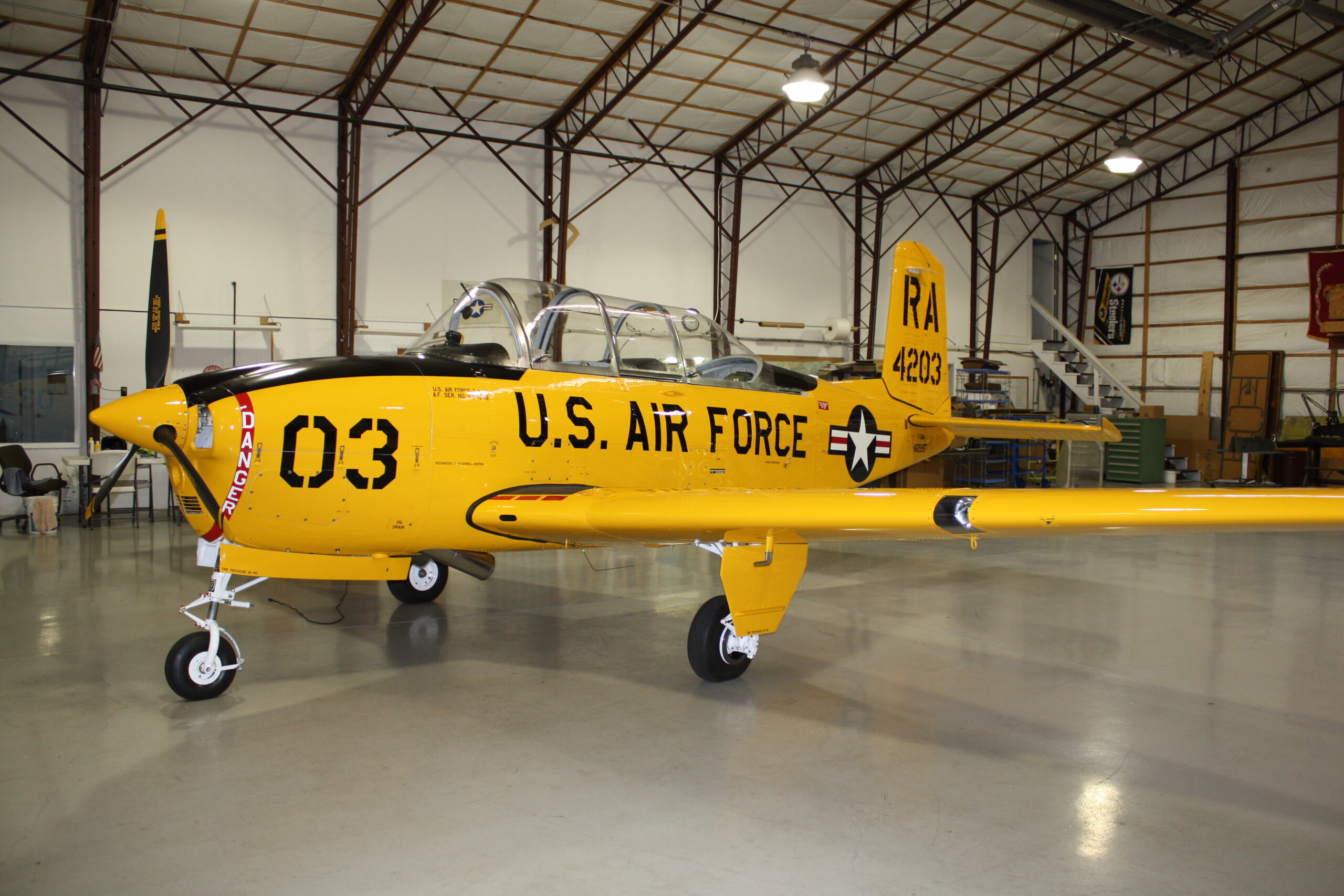
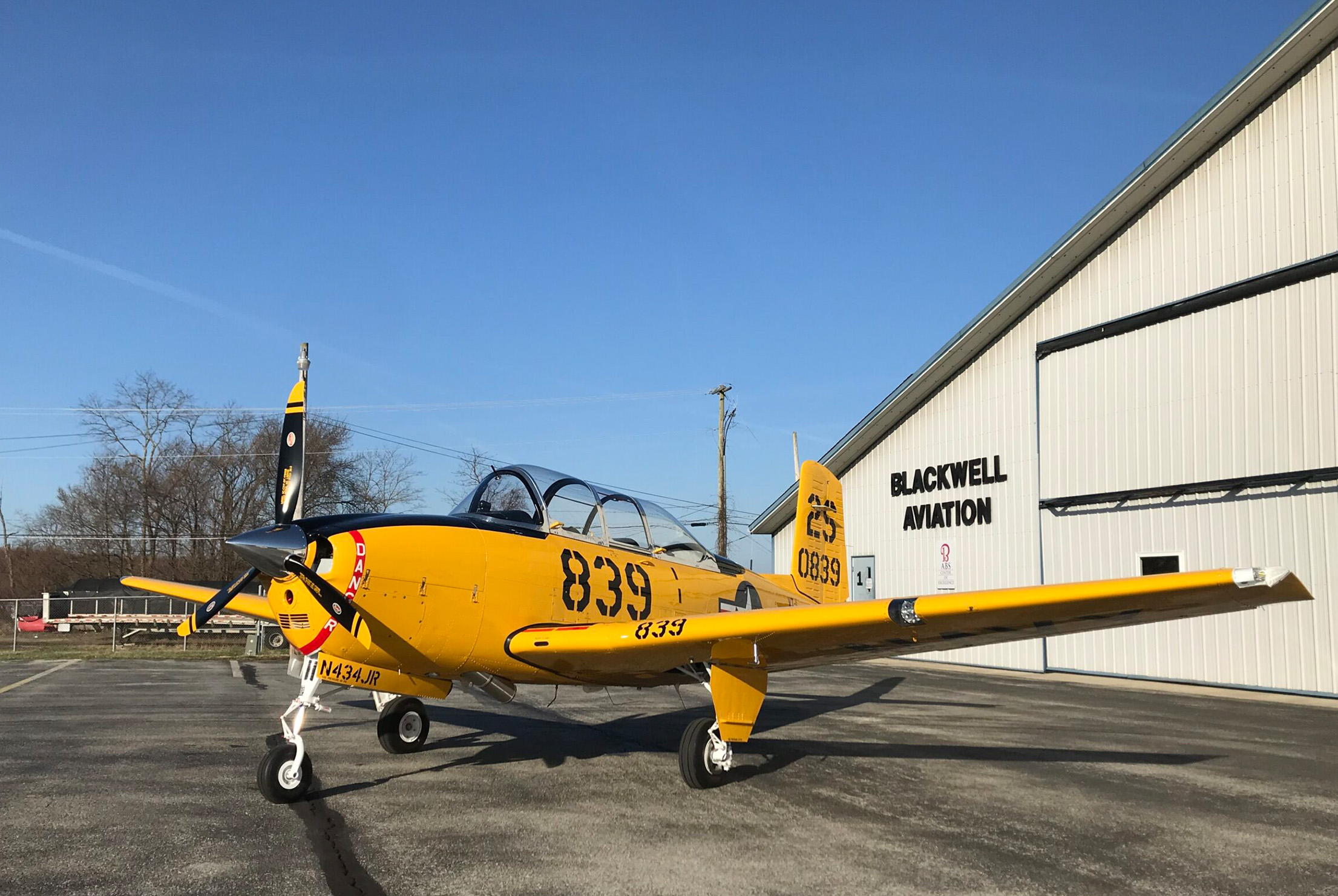
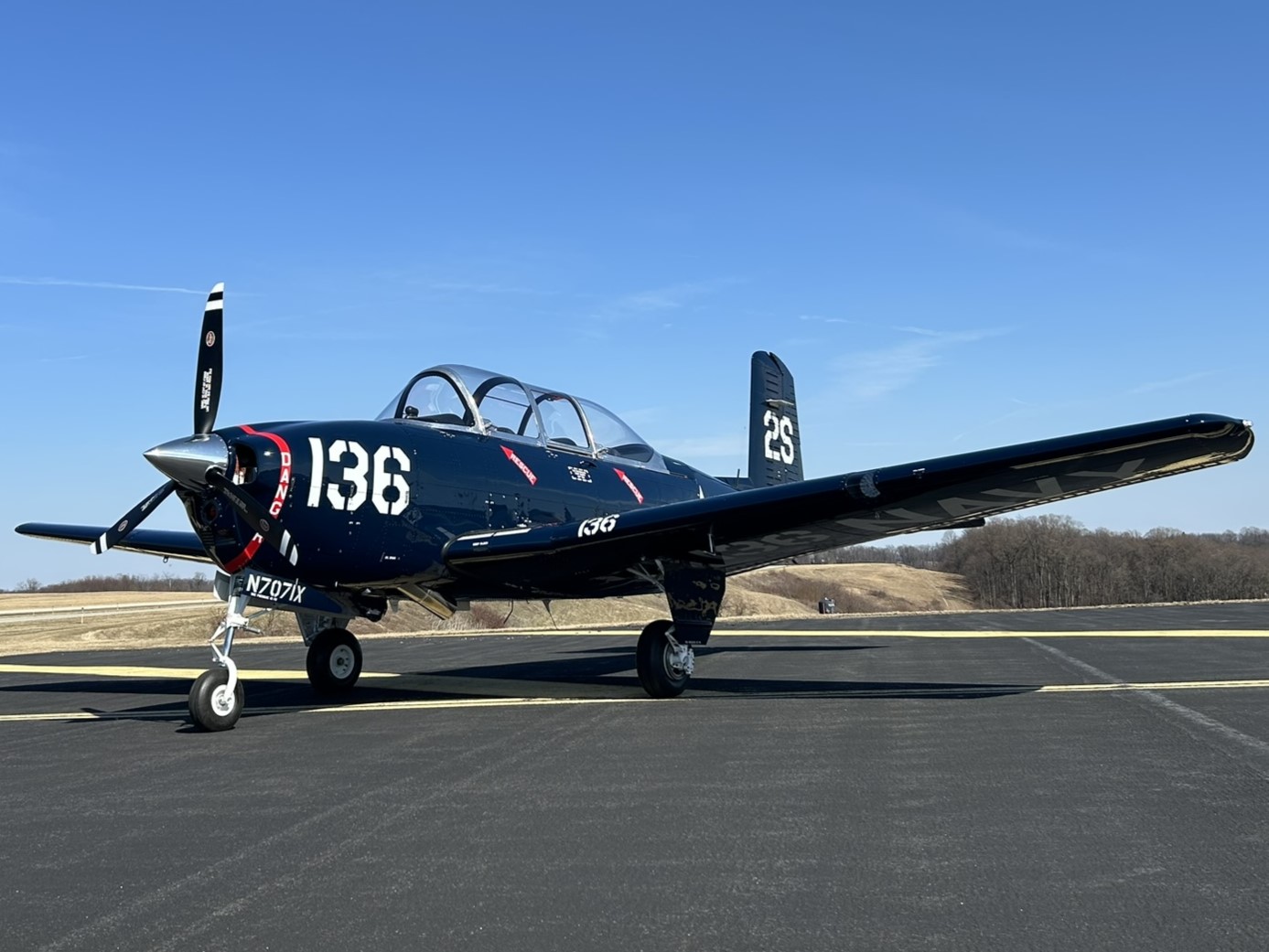
We also sell many new or overhauled parts such as:
Engines
Propellers
Heavy duty main landing gear retract rods
Custom seat cushion sets
Landing gear dust boots
Stick grip boots
Cleveland 8” wheel and brake kits
Wing root seals
Fuel Cells
Fuel Valves
Fuel Dukes pump conversion kits
Digital fuel level senders
JPI digital engine monitors
Engine control cables
Flight and trim control cables
Wire harnesses
Landing gear and flap motors